3.1. Расчёт эффективного фонда времени работы оборудования
Вначале определяется календарный фонд времени дней.
Затем определяется номинальный фонд времени работы оборудования:
,
где FП — количество выходных и праздничных дней (причём следует учитывать, что в Беларуси на данный момент 9 официальных праздничных дней: 1, 7 января, 8 марта, Радуница, 1, 9 мая, 3 июля, 7 ноября, 25 декабря).
В часах номинальный годовой фонд времени работы оборудования при работе в одну смену равен
,
где — количество полных рабочих дней;
— количество предпраздничных, сокращённых на 1 ч дней;
— продолжительность рабочей смены, ч ;
— продолжительность предпраздничной рабочей смены, ч .
Годовой эффективный фонд времени работы оборудования в часах определяется по формуле
где
— коэффициент, учитывающий время простоя
оборудования в плановом ремонте (для
уникальных станков и станков свыше 30-й
категории сложности,
для станков с ЧПУ,
для обрабатывающих центров
).
Годовой эффективный фонд времени в днях с учётом простоев оборудования в плановых ремонтах определяется по формуле
.
3.2. Расчёт количества партий деталей и количества переналадок оборудования
Количество партий деталей зависит от номенклатуры обрабатываемых деталей и от количества дней (смен) работы оборудования , если принять, что запуск (выпуск) всех видов деталей будет осуществляться ежедневно (ежесменно). Для базового варианта . В связи с тем что организация работы гибкого автоматизированного производства не требует большой численности рабочих-операторов и участок оснащён весьма дорогостоящим оборудованием, целесообразно осуществлять производственный процесс в три смены . При ежесменном запуске деталей количество партий определяется по формуле
,
где — число рабочих смен в сутки.
Количество переналадок оборудования на каждой операции будет равно количеству партий деталей:
.
3.3. Расчёт годового фонда времени, затрачиваемого на переналадку оборудования
Расчёт ведётся по формуле
ч,
где — время на переналадку оборудования на соответствующей операции, устанавливаемое на партию деталей, мин;
— количество переналадок оборудования на соответствующей операции в течение планового периода.
Расчёт фонда времени, затрачиваемого на переналадку оборудования, производится в табличной форме (табл. 3.1).
Таблица 3.1
Расчёт фонда времени, затрачиваемого на переналадку оборудования
Наименование операций | Базовый вариант | Проектируемый вариант | ||||
, мин | ,
шт. | , ч | , мин | , шт. | , ч | |
1.Токарная 1 | 4,5 | 1616 | 121,2 | 2,5 | 2424 | 101 |
2.Токарная 2 | 4,5 | 1616 | 121,2 | 2,5 | 2424 | 101 |
3. | … | … | … | … | … |
3.4. Расчёт производственной программы
Гибкие производственные участки обычно создаются для обработки деталей различных типоразмеров, которые используются для изготовления изделия. Следовательно, программы выпуска по каждому типоразмеру или равны, или кратны между собой.
Если программы по типоразмерам равны, т.е. , то их величину можно определить исходя из следующего уравнения:
,
,
,
где — программаj-го типоразмера деталей на плановый (годовой) период времени, шт.;
—
оперативное время по каждому типоразмеру
деталей по ведущей группе оборудования
проектируемого варианта, по которой
определяется мощность участка по
отдельной операции технологического
процесса, мин.
Если программы по типоразмерам не равны, но кратны, то их величину можно определить исходя из выражения
,
,
,
; ; … ;.
За ведущую группу оборудования обычно принимается наиболее дорогостоящее, однако это зачастую приводит к низкой загрузке оборудования на других операциях. Поэтому, если спрос на продукцию предприятия достаточно велик, можно для повышения загрузки оборудования на всех операциях за ведущую группу принимать оборудование на той операции, у которой суммарное оперативное время по всей номенклатуре деталей наименьшее.
Фонд времени работы оборудования плановый
ФОНД ВРЕМЕНИ РАБОТЫ ОБОРУДОВАНИЯ — плановое количество часов работы оборудования в течение определенного календарного периода (год, квартал, месяц). Ф. в. р. о. рассчитывают для определения производств, мощности пром. предприятия (цеха, участка), потребного количества оборудования при проектировании предприятий, цехов, а также выявления уровня использования оборудования на дей- [c.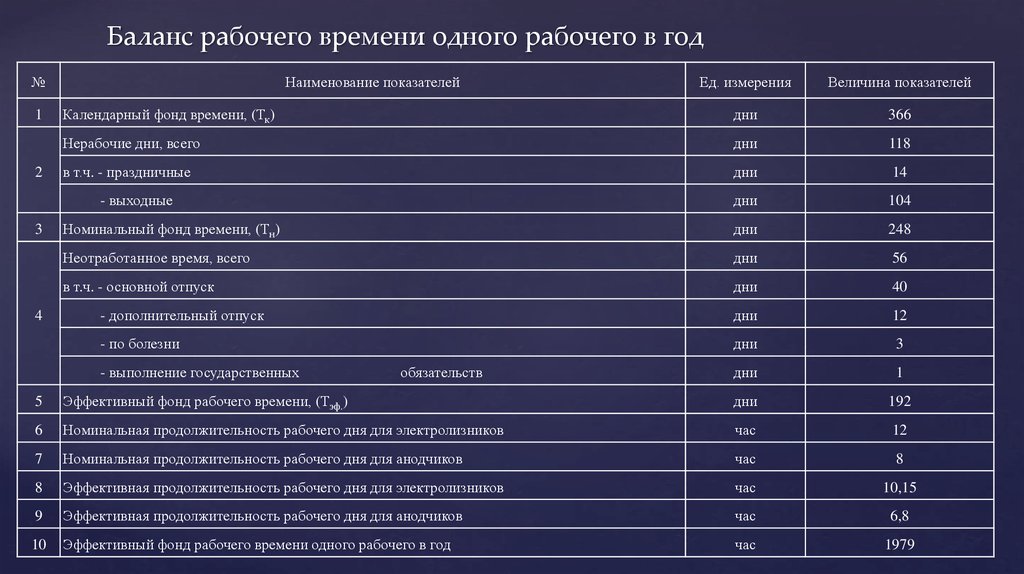
Действительный (располагаемый) годовой фонд времени работы оборудования Ф определяется как разность между режимным фондом Гр и фондом времени, необходимым для проведения плановых ремонтов Тия, р [c.108]
Для участков с прерывным процессом производства эффективный фонд времени работы оборудования определяется исходя из установленной сменности работы и продолжительности смены с учетом простоя оборудования при проведении планово-предупредительных ремонтов и сокращения работы в предпраздничные дни [c.102]
Плановый фонд времени работы оборудования зависит от частоты и длительности ремонта. Существенное влияние на частоту и длительность ремонтов технологических установок оказывает качество сырья, главным образом содержание в нем серы. Например, установки прямой перегонки нефти на заводах Азербайджана подвергаются капитальному ремонту в среднем один раз в четыре года, а на заводах Башкирии ежегодно, значительно реже ремонтируются в Азербайджане и установки термического и каталитического крекинга.
Однако на предприятии А производительность линии по выпуску петлевых покрытий ниже, чем часовой выпуск покрытий ворсового типа. Кроме того, лимитирующим фактором является плановый фонд времени работы оборудования. Линии по производству ковровых покрытий могут работать лишь в течение 2000 ч. Эта информация представлена в табл. 4.8. [c.237]
Режимное время составляет 98,5 % планового (11178,5 11348,7 х х 100). Разный процент использования календарного (99,2 %) и режимного (98,5 %) фондов времени работы оборудования свидетельствует о том, что фактическое количество рабочих дней и коэффициент сменности были ниже предусмотренных планом. [c.317]
Данные табл. 7.10 позволяют выявить влияние изменений количества действующего оборудования, продолжительности (времени) работы единицы оборудования и его производительности на объем продукции (табл. 7.15). Соблюдая плановые пропорции, предприятие могло иметь дополнительный выпуск продукции на 313145,9 тыс. р. (18695,3 + + 294450,6), но эти возможности оно упустило. Особенно плохо использован плановый фонд времени работы оборудования, что привело к уменьшению выпуска продукции на 294450,6 тыс. р., или на 2480 %. В то же время благодаря росту производительности оборудования получен дополнительный выпуск продукции на 325018,9 тыс. р., или на 2737,5 %.
[c.320]
Производственная возможность группы однородного оборудования Хгр определяется отношением суммарного действительного годового фонда времени работы оборудования fn к суммарной трудоемкости планового выпуска изделий, обрабатываемых на данном оборудовании, ZK [c.146]
Действительный фонд времени работы оборудования равен режимному за вычетом времени на планово-предупредительный ремонт. [c.39]
Если цехи, участки и рабочие места оснащены оборудованием, не требующим планового ремонта в рабочее время, действительный фонд времени работы оборудования и использования производственных площадей этих подразделений принимается равным режимному фонду.
[c.39]
Расчетно-аналитический, основанный на установлении средней продолжительности изготовления одной партии предметов труда между двумя переналадками. Эта продолжительность определяется как отношение фонда времени работы оборудования за плановый период к числу переналадок. Время ожидания принимается равным половине этой величины. [c.87]
Вместо одного используемого показателя интегральной нагрузки работы оборудования, определяемого как произведение коэффициента экстенсивной нагрузки, исчисленного к плановому фонду времени работы оборудования, и коэффициента плановой интенсивной нагрузки оборудования предлагается ввести два интегральных показателя [c.322]
Плановый резервный фонд времени работы оборудования Фактический резервный фонд времени работы оборудования [c.326]
КОЭФФИЦИЕНТ ЗАГРУЗКИ ОБОРУДОВАНИЯ — относительный показатель, характеризующий использование действительного (эффективного) фонда времени работы оборудования в течение определенного времени (планового, отчетного периода). Рассчитывается на основе производственной программы (плановых заданий) и технических норм времени обработки изделий (деталей) на данном оборудовании. Плановый К.з.о. (К3) находят по формуле [c.174]
Уровень использования планового фонда времени определяется отношением фактически отработанного времени к плановому фонду времени работы оборудования. [c.49]
Основной причиной недоиспользования планового фонда времени работы оборудования является наличие значительных простоев оборудования как по вине предприятия (отсутствие рабо- [c.49]
Фонд времени работы оборудования и режим работы предприятия. При расчете П.м. предприятия принимается максимально возможный плановый (эффективный) годовой фонд времени работы оборудования. Для агрегатов непрерывного действия (доменные и мартеновские печи, химические [c.223]
При определении действительного (расчетного годового фонда времени работ оборудования из номинального фонда) времени исключают затраты времени на пребывание оборудования в плановых ремонтах, установленные утвержденными нормами системы планово-предупредительных ремонтов.
[c.39]
При определении различных показателей экстенсивной загрузки оборудования, а также производственной мощности объединения, предприятия, цеха в качестве исходных данных принимается фонд времени работы оборудования. Принято различать следующие фонды времени работы оборудования календарный, режимный (номинальный), плановый (эффективный) и фактический, которые определяются на единицу или группу установленного оборудования. [c.87]
Коэффициент использования планового фонда времени работы оборудования R» определяется следующим образом [c.89]
Коэффициент использования планового фонда времени работы оборудования [c.127]
Расчету производственной мощности предшествует установление или уточнение исходных данных и подбор исходной информации для расчета установление или уточнение номенклатуры и планового или расчетного ассортимента продукции определение количества оборудования, принимаемого в расчет установление перечня видов ведущего оборудования, ведущих участков и цехов отбор исходных данных и нормативов для расчета фонда времени работы оборудования и прогрессивных показателей его производительности (или норм затрат машинного, аппаратурного времени на единицу продукции) уточнение планового (проектируемого) объема выпуска продукции по централизованным заданиям подбор данных для определения направления и меры влияния намечаемых реконструкций, технического перевооружения и оргтехме-роприятий на величину производственной мощности, подбор данных для пересчета мощности в соответствующие единицы измерения и т. д.
[c.146]
При наличии на предприятии прерывного (эпизодического) процесса производства максимально возможный годовой фонд времени работы оборудования определяется исходя из трехсменного, а при работе в четыре смены—четырехсменного режима работы оборудования с учетом установленной продолжительности смены в часах. Из рассчитанной по такой методике величины годового фонда работы оборудования вычитается время на плановые ремонты по нормативу, время выходных и праздничных дней, а также нерабочее время в сокращенные, предпраздничные и предвыходные дни. Сели ведущие цехи предприятия работают в две или меньше смены, тогда расчет производственной мощности производится исходя из двухсменного режима работы. [c.112]
Определяя производственную структуру цеха наряду с составом и характером основных участков, необходимо знать состав входящих в него вспомогательных участков (ремонтного, заточного и др.), и служб (инструментально-раздаточная кладовая, межоперационные и комплектовочные кладовые, слуисба технического контроля, лаборатории и др. ). Производственная структура участка зависит от состава деталей, закрепляемых за ним, принятых форм разделения труда между участками, технологических процессов изготовления изделий, состава и количества оборудования и рабочей силы. К организационно-плановым показателям, подлежащим расчету при проектировании цехов и участков, относятся ритм работы, коэффициент синхронности выполнения отдельных операций и их комплекса, размер партий деталей, периодичности запуска партий деталей в производство, длительность производственного цикла партий деталей и изделий, коэффициент непрерывности процесса, фонды времени работы оборудования, коэффициент использования оборудования и др. (см. 4.2, 5.1 и 5.2).
[c.60]
Действительный годовой фонд времени работы оборудования Рл рассчитывается в зависимости от количества рабочих дней в году, числа смен работы, длительности одной смены и плановых простоев оборудования, предусмотренных посистеме планово-предупредительного ремонта. [c.33]
Для предприятий с прерывным процессом производства учитывается календарный фонд времени работы оборудования исходя из двух-, трех- или четырехсменного режима, если предприятие работает в четыре смены, режима и установленной продолжительности смен в часах за вычетом времени, необходимого на проведение капитальных и планово-предупредительных ремонтов, времени выходных и праздничных дней, сокращения рабочего времени в праздничные дни.
[c.303]
ФОНД ВРЕМЕНИ РАБОТЫ ОБОРУДОВАНИЯ — потенциаль-ная или фактическая продолжительность работы оборудования в плановом периоде. Различают Ф. в. р. о. календарный, режимный (номинальный), эффективный (нормативный, плановый), фактический. Календарный Ф. в. р. о. определяется астрономическим числом часов в рассматриваемом периоде. Режимный Ф. в. р. о. определяется путем вычета из календарного фонда нерабочего времени с учетом сменности работы оборудования и установленных перерывов в работе в течение суток. Эффективный Ф. в. р. о. рассчитывается на основе режимного за вычетом плановых простоев оборудования в ремонте, а также затрат времени на его наладку и переналадку. Фактический Ф. в. р. о. может быть меньше эффективного на величину сверхплановых простоев и больше его на величину сверхурочных часов (см. также Коэффициент сменности). [c.352]
Что такое эффективный фонд рабочего времени оборудования?
Заглавная страница
КАТЕГОРИИ: Археология ТОП 10 на сайте Приготовление дезинфицирующих растворов различной концентрации Техника нижней прямой подачи мяча. Франко-прусская война (причины и последствия) Организация работы процедурного кабинета Смысловое и механическое запоминание, их место и роль в усвоении знаний Коммуникативные барьеры и пути их преодоления Обработка изделий медицинского назначения многократного применения Образцы текста публицистического стиля Четыре типа изменения баланса Задачи с ответами для Всероссийской олимпиады по праву Мы поможем в написании ваших работ! ЗНАЕТЕ ЛИ ВЫ? Влияние общества на человека Приготовление дезинфицирующих растворов различной концентрации Практические работы по географии для 6 класса Организация работы процедурного кабинета Изменения в неживой природе осенью Уборка процедурного кабинета Сольфеджио. Все правила по сольфеджио Балочные системы. |
⇐ ПредыдущаяСтр 2 из 8Следующая ⇒ Эффективный и действительный – это один и то же фонд.
Чем отличаются эти показатели и как рассчитываются? Календарный: (дни в году)*24, номинальный равен произведению рабочих дней в году на продолжительность смены, на длтельность смены. Номинальный с учётом праздничных дней: Фр = С * [(Дк – Двых) * Тсм – (Чн * Дпред)], где Дк — количество календарных дней в году; Двых – число выходных и праздничных дней в периоде; Тсм – длительность рабочей смены, ч.; Чн – количество нерабочих часов в предпраздничные дни; Дпред – количество предпраздничных дней в периоде. Эффективный (плановый, действительный) фонд времени (Фэф) рассчитывается исходя из режимного с учетом остановок на ремонт: Фэф = Фр * (1 – α /100), где α – процент потерь рабочего времени на выполнение плановых ремонтных операций и межремонтного обслуживания (составляет 2-12%). Определение расчетного количества единиц основного оборудования j-ого вида (nрасчj) выполняется по формуле: , где Тj– трудоемкость производственной программы цеха на основном оборудовании j-ого вида, нормо-час. Показатель nрасчj округлить до десятых долей. nрасч_токарные=10840/930=11,7 nрасч_револьверные=10340/930=11,1 nрасч_фрезерноые=10800/930=11,6 nрасч_сверлильные=6170/930=7 nрасч_слесарные=12770/930=11,6 Поскольку расчетное количество основного оборудования получается дробным, то его округляют до ближайшего целого числа в большую сторону и получают принятое количество оборудования. Всегда ли такой вариант округления показателя nрасчj является правильным? Зависит от экономической выгоды предприятия, возможности получения экономической выгоды и выполнения требуемой работы в срок. Определение принятого количества основного оборудованияпо j-ой группе оборудования (nоснпрj) и суммарного количества основного оборудования в цехе. Поскольку расчетное количество основного оборудования получается дробным, то его округляют до ближайшего целого числа в большую сторону и получают принятое количество оборудования – nоснпрj. nоснпр_токарные=12 nоснпр__револьверные=12 nоснпр_фрезерноые=12 nоснпр_сверлильные=7 nоснпр_слесарные=12 Коэффициент загрузки оборудования j-ого вида (kзагрj) рассчитывают, используя следующую формулу: kзагрj=nрасчj/nоснрj. Показатель kзагрj округляется до сотых долей. kзагр_токарные=11,7/12=0,98 kзагр__револьверные=11,1/12=0,93 kзагр_фрезерноые=11,6/12=0,97 kзагр_сверлильные=6,6/7=0,94 kзагр_слесарные=11,6/12=0,97
При принятии каких управленческих решений используется коэффициент загрузки оборудования? Коэффициент загрузки оборудования используется при принятии решений по эксплуатации оборудования, в том числе, сменности производства. Определение средней загрузки основного оборудования в цехе (kзагрцех) по формуле: , показатель kзагрцех округляется до сотых долей. kзагрцех=(11,7+11,1+11,6+6,6+11,6)/(12+12+12+7+12)=0,96.
⇐ Предыдущая12345678Следующая ⇒ Читайте также: Организация работы процедурного кабинета Статус республик в составе РФ Понятие финансов, их функции и особенности Сущность демографической политии |
Последнее изменение этой страницы: 2016-12-10; просмотров: 965; Нарушение авторского права страницы; Мы поможем в написании вашей работы! infopedia. |
Преимущества общей эффективности оборудования (OEE)
Общая эффективность оборудования (OEE) изначально описывалась как центральный компонент общего производственного обслуживания (TPM) для производства товаров без дефектов и без потерь. Общая цель TPM — добиться наиболее оптимального производственного процесса за счет повышения производительности, эффективности и безопасности.
Что такое общая эффективность оборудования?
Общая эффективность оборудования (OEE) — это мера того, насколько хорошо используется производственная операция по сравнению с ее полным потенциалом. Это помогает производителям определить области производства, которые действительно эффективны и продуктивны, а какие области нуждаются в улучшении.
Значение OEE представлено в процентах. Оценка 100% означает, что вы используете свои ресурсы в полной мере. Другими словами, вы производите качественную продукцию быстро, практически без простоя оборудования.
Любое значение ниже 100% считается возможностью для улучшения, что является одной из основных целей общего обслуживания производства. Использование OEE может быть чрезвычайно полезным для вашей работы и может выявить потери, прогресс и различные методы потенциального повышения производительности оборудования. Есть много преимуществ, которые вы получите, если рассчитаете общую эффективность оборудования вашей производственной операции.
Преимущества общей эффективности оборудования (OEE)
Вот преимущества использования общей эффективности оборудования (OEE):
1. Визуализация производительности
Наиболее очевидным преимуществом расчета OEE является то, что вы сможете легко визуализировать производительность вашего производства. Это связано с тем, что общая эффективность оборудования рассматривает неэффективность производства и потери в трех областях: доступность, производительность и качество. Затем эти значения группируются в единую метрику, которая показывает текущее состояние производства и области, нуждающиеся в улучшении.
2. Анализ производства
Невозможно узнать реальное состояние вашего производства без его измерения. Часто производители предполагают, что эффективность их процессов намного выше, чем она есть на самом деле. Это потому, что вы не можете управлять или улучшать то, что не измеряется. Когда вы проанализируете свои производственные показатели и потери производительности, вы будете лучше понимать, какие области вашего производства работают с максимальной эффективностью, а какие области нуждаются в улучшении.
3. Повышение конкурентоспособности
Производственный рынок характеризуется высокой конкуренцией, и многие производители и потребители влияют на производимые продукты. Производители должны стремиться сохранить конкурентное преимущество, чтобы увеличить свою прибыль. Общая эффективность оборудования может помочь производителям повысить свою конкурентоспособность, выделив области, которые нуждаются в улучшении. В результате производственные операции смогут снизить себестоимость продукции и поставлять своим клиентам продукт высокого качества. Имея лучшую стоимость и качество, чем их конкуренты, производители сохранят свое конкурентное преимущество на рынке.
4. Снижение стоимости оборудования
Понимание фактической производительности вашего оборудования напрямую связано с пониманием того, работает ли оно эффективно или нет. Он также заблаговременно определяет, есть ли проблемы, которые могут привести к необходимости ремонта в будущем, и может помочь предотвратить возникновение крупных поломок. С помощью функции «Общая эффективность оборудования» вы сможете предвидеть события, которые чрезвычайно дорого обходятся производственным предприятиям, например отказы оборудования, и сможете планировать профилактическое обслуживание в стратегически важные моменты. Кроме того, оптимизировав свое производство, вы сможете сократить время, в течение которого дорогостоящие машины простаивают и ожидают завершения предшествующих операций.
5. Возврат инвестиций (ROI)
Машины и оборудование представляют собой крупные инвестиции, сделанные компаниями для достижения максимальной отдачи от инвестиций. Общая эффективность оборудования в первую очередь поможет производителям определить наилучшую область для вложения средств. Кроме того, расчеты OEE помогут предприятию сравнить производительность до и после добавления нового оборудования, а также убедиться, что новая машина используется по назначению. весь потенциал. Операторы могут подтвердить финансовую ценность этих инвестиций с помощью измеримых данных, обеспечиваемых общей эффективностью оборудования (OEE).
Как рассчитать общую эффективность оборудования (OEE)
Формула для расчета общей эффективности оборудования следующая:
OEE = доступность (A) x производительность (P) x качество (Q)
0
00 Три компонента — доступность, производительность и качество — представляют области, которые несут наибольшие потери. Плохое качество продукции с большим количеством дефектов, низкая производительность и множество остановок и запусков делают систему непроизводительной. Каждый компонент уравнения также имеет свое определение и расчет:
- Наличие (А)
- Доступность (A) = Время работы / Запланированное время производства
- Этот компонент учитывает все события, препятствующие запуску производства. Сюда могут входить запланированные остановки, такие как переналадка и время наладки, или незапланированные остановки, такие как поломки оборудования.
- Производительность (P)
- Производительность (P) = (Идеальное время цикла x Общее количество) / Время работы
- Этот компонент учитывает все события, из-за которых производительность производства снижается до максимально возможной.
- Качество (Q)
- Качество (Q) = (Производные единицы — Дефекты) / Произведенные единицы
- Этот компонент учитывает все произведенные товары, которые не соответствуют желаемым стандартам качества или нуждаются в доработке.
Расчет общей эффективности оборудования позволит вам определить области на вашем производственном объекте, которые являются причиной вашей неэффективности. После расчета OEE программное обеспечение Advanced Planning and Scheduling (APS) может помочь вам оптимизировать производственный график, чтобы свести к минимуму время простоя и увеличить производительность.
Еще одним преимуществом PlanetTogether APS является возможность интегрировать графики профилактического обслуживания с производственными графиками. Обязательства не могут быть выполнены без максимизации общей эффективности оборудования (OEE). Возможность выделить время для профилактического обслуживания до того, как график будет заполнен заказами, увеличивает время безотказной работы и производительность.ГЭРИ БИШОП, ДИРЕКТОР ПО ПРОИЗВОДСТВУ, SUMITOMO ELECTRIC LIGHTWAVE
Программное обеспечение для расширенного планирования и планирования (APS)
Программное обеспечение для расширенного планирования и составления графиков стало обязательным для современных производственных операций, поскольку спрос клиентов на расширение ассортимента продукции, быструю доставку и снижение цен становится преобладающим. Эти системы помогают планировщикам экономить время, обеспечивая большую гибкость при обновлении постоянно меняющихся приоритетов, производственных графиков и планов запасов. Системы APS можно быстро интегрировать с программным обеспечением ERP/MRP, чтобы заполнить пробелы, где этим системам не хватает гибкости, точности и эффективности планирования и планирования.
С PlanetTogether APS вы можете:
- Создавать оптимизированные графики, которые уравновешивают эффективность производства и производительность доставки
- Максимально увеличить пропускную способность узких мест ресурсов для увеличения дохода
- Синхронизация предложения со спросом для сокращения запасов
- Обеспечьте доступность ресурсов в масштабах всей компании
- Включить принятие решений на основе данных сценария
Внедрение программного обеспечения Advanced Planning and Scheduling (APS) выведет ваши производственные операции на новый уровень эффективности производства за счет использования оперативных данных, которые уже имеются в вашей ERP-системе. APS — это шаг в правильном направлении повышения эффективности и бережливого производства. Попробуйте бесплатную пробную или демо-версию!
Ресурсы APS
Инфографика
Практические примеры
Белые книги
Темы: Расширенное планирование и планирование, Преимущества АПС, ОЕЕ
Расчет общей эффективности оборудования (OEE)
Общая эффективность оборудования (OEE) является частью процесса повышения эффективности производства. Термин бережливого производства, разработанный японцами, в частности, Сейити Накадзимой, — OEE устанавливает порядок определения эффективности каждого этапа операции в производстве. OEE — это показатель, определяющий процент действительно продуктивного времени.
Чтобы дать вам представление о том, как работает подсчет баллов: 100 % — это идеальное производство, 85 % — это производство мирового класса, 60 % — это довольно типично, 40 % — нет. необычно для производителей, которые не практикуют методы бережливого производства (TPM — Total Productive Maintenance). Расчет OEE поможет вашей компании определить, где улучшить качество, где максимально использовать имеющиеся ресурсы и сократить количество отходов, что сэкономит вам деньги в долгосрочной перспективе.
Вот гипотетический пример: Завод по производству шин недавно внедрил Кайдзен, бережливый процесс постоянного улучшения. После того, как Кайдзен был полностью внедрен, каждый сотрудник теперь мотивирован оценивать этапы своей работы, чтобы повысить эффективность. Сотрудники заметили, что на каждые 100 шин, произведенных на производственной линии; есть группа из 12-14 шин, которые заканчиваются неправильно нарезанными протекторами. До внедрения Кайдзен сотрудники считали эти шины бракованными, предполагая, что это была обычная погрешность. Поскольку все сотрудники теперь ищут способы постоянного улучшения процесса, OEE используется для оценки каждого шага в процессе производства шин, чтобы определить, где можно сделать улучшения. Проблема синхронизации была обнаружена на одном этапе процесса, когда машина перезагружалась в течение дополнительных четырех минут, в то время как шины продолжали движение по линии. Это вызвало небольшую партию каждые 90 минут неправильно нарезать шины. С помощью OEE было определено, что производственная линия замедлится на эти 4 минуты. Эта корректировка повысила показатель качества, сократив количество отходов.
Решение об обновлении конкретной машины было принято на основе расчета OEE .
*Расчет OEE основан на трех факторах; Доступность (A), производительность (P) и качество (Q). Как рассчитывается каждый?
Доступность учитывает Потеря времени простоя.
A = Время работы / Плановое время производства
Пример: Конвейерная система должна работать две смены по 8 часов (960 минут) с 30-минутным перерывом каждые 8 часов.
Время работы = 900 минут запланированных — 90 минут незапланированных простоев = 810 минут
Расчет: Доступность = Время работы / Плановое время производства
Доступность 810 минут / 900 = 90%
Производительность учитывает Потеря скорости
P = Идеальное время цикла / (Время работы/общее количество штук)
Идеальное время цикла — это минимальное время цикла, которого можно ожидать от вашего процесса в оптимальных условиях. Иногда его называют Расчетное время цикла, Теоретическое время цикла или Паспортная мощность.
Пример: Конвейерная система должна работать две смены по 8 часов (960 минут) с 30-минутным перерывом каждые 8 часов.
Время работы = 900 минут запланированных — 90 минут незапланированных простоев = 810 минут
Детали производятся со стандартной скоростью 40 единиц в час или 1,5 минуты на единицу
Конвейерная система производит 525 единиц в течение всего дня. Это Total Units, а не Good Units. Качество здесь не измеряется.
Расчет: Производительность = Идеальное время цикла / (время работы всех деталей)
Время изготовления деталей = 525 * 1,5 минуты на единицу = 787 минут (идеальное время цикла)
Производительность (производительность) = 787 /810 = 97%
Качество рассматривает Потеря качества, и рассчитывается как:
Q = Хорошие пьесы / Общие пьесы
(525 произведенных единиц — 39 дефектных единиц) = 469 единиц
469 исправных единиц / 525 всего произведенных единиц = 89%0145 OEE = Доступность x Производительность x Качество
*Формула расчета взята с сайта www. oee.com. Примеры гипотетические.
Использование OEE не является абсолютным показателем; он может ломаться в разных областях. Его лучше всего использовать для выявления проблемных областей, которые потребуют дальнейшего анализа для повышения ключевой производительности. От ручных, полуавтоматических до полностью автоматических операций или процессов, внедрение инструментов OEE в рамках вашего протокола бережливого производства повысит производительность любого процесса на вашем рабочем месте.
OEE зависит от сокращения времени простоя машин и систем. Узнайте о наших рекомендуемых передовых методах в Total Productive Maintenance Guide, где мы даем практические советы по повышению производительности и безопасности вашей организации. Получите бесплатную копию ниже!
Videojet Productivity Pulse™ — финансовое обоснование поддержки OEE и постоянного улучшения
Финансовое обоснование поддержки OEE и непрерывного совершенствования
OEE имеет значение, только если вы занимаетесь производственной стороной бизнеса, верно? Улучшение практических результатов имеет первостепенное значение для роста бизнеса, как и постоянное совершенствование. Внедрение OEE и программы постоянного улучшения может положительно повлиять на эффективность вашего производства и сократить расходы. Итак, давайте обсудим, как метрики, основанные на OEE, и использование программ непрерывного улучшения (CI) могут помочь вам:
- Сокращение отходов и затрат
- Предоставление основанного на фактах обоснования нового оборудования
Как именно вы можете использовать OEE для внесения этих улучшений?
Снижение отходов/затрат
Использование показателей OEE и программы CI может помочь вам увеличить производительность. Однако ценность увеличения объема производства основывается на одном важном допущении: вы можете продать все произведенные дополнительные единицы продукции. Но что, если это не так, какую финансовую выгоду можно получить?
Повышение эффективности производства вашей продукции, даже если у вас нет существующей необходимости производить больше продукции с текущими ресурсами, означает, что вы можете сократить количество отходов и затрат, получив значительные преимущества в следующих областях:
Меньше рабочей силы : Повышение эффективности производство может позволить вам сократить количество сверхурочных часов, особенно если вы можете исправить линии или продукты, которые демонстрируют значительные ежедневные отклонения. Со временем это может позволить вам консолидировать производство, закрыть менее производительные линии и сократить общий объем труда на заводе.
Меньше затрат на техническое обслуживание : Понимание первопричин самых крупных простоев может помочь вам упреждающе решать эти проблемы и сокращать количество случаев, требующих вмешательства по техобслуживанию. Хотя в краткосрочной перспективе могут возникнуть некоторые дополнительные первоначальные затраты, это приведет как к сокращению затрат на детали, связанные с техническим обслуживанием, так и к затратам на оплату труда. Даже если вы считаете общие затраты на техническое обслуживание в основном фиксированными, повышение эффективности принесет финансовую выгоду.
Меньше отходов, выше качество : Отбракованный продукт имеет сопутствующие расходы, будь то ремонтные работы или отходы упаковки/продукта. В приведенном ниже сценарии план OEE и CI, который может обеспечить качество 96%, даст экономию в размере 240 единиц x связанные затраты на каждую единицу этого продукта.
Этот пример (8-часовая смена без запланированного простоя) иллюстрирует влияние дополнительного производства, фокусируясь на чистом выпуске, который составляет 5 760, что на 2 840 единиц меньше запланированного для смены.
Основанное на фактах обоснование нового оборудования
Все производственные компании испытали «борьбу», которая существует в процессе подачи заявки на приобретение капитала. Операции обычно предрасположены к тому, чтобы иметь более новое оборудование и большую мощность, в то время как финансы отвечают за обеспечение того, чтобы капитал распределялся по мере необходимости с соответствующей окупаемостью инвестиций. Этот процесс становится более обременительным, когда нет стандартизированного, объективного набора данных, с которым могут согласовываться операции и финансы. OEE может предоставить эти данные. Когда данные стандартизированы, собраны и объединены с основными деталями, которые должны быть зафиксированы как часть вашей программы CI, появляется четкий ответ на вопрос, нужен ли новый капитал.
Давайте рассмотрим два примера:
Увеличение производительности оборудования : Когда требуется дополнительная производительность завода, просмотр оценок OEE для завода и отдельных производственных линий, чтобы понять, насколько вы близки к 100%, является хорошим стартовый индикатор. 50-е и 60-е баллы, безусловно, указывают на то, что повышение эффективности, вероятно, является лучшим путем, чем капитальные затраты. С OEE «мирового класса», вероятно, потребуется провести анализ того, насколько реалистичным может быть достижение дальнейшего существенного выигрыша. Баллы выше 90% являются хорошим признаком того, что приобретение дополнительного капитала, вероятно, оправдано.
Но важно помнить, что контекст для OEE — это Запланированное время производства , поэтому, прежде чем приобретать дополнительное оборудование, вам нужно ответить на вопрос «Должен ли я или могу просто планировать увеличение времени производства?». Для этого типа решения можно использовать вариант OEE под названием Total Effective Equipment Performance (TEEP). TEEP добавляет четвертый компонент к уравнению OEE, который представляет собой процент запланированного времени производства по сравнению с общим количеством времени в день. Зная это значение, можно выделить активы, которые недоиспользуются во время существующих смен. Если это число также относительно велико, и вы еще не работаете в 3 смены, вам нужно подумать, добавить ли еще одну смену. Конечно, дополнительные смены сопряжены с дополнительными затратами, которые следует сравнивать со стоимостью нового капитала. Хотя данные OEE будут играть минимальную роль в этом расчете, наличие системы измерения OEE может помочь различным заинтересованным сторонам пройти через процесс принятия решений, чтобы они пришли к согласованному моменту.
Замена существующего оборудования : Измерения OEE могут пролить свет на оборудование, которое постоянно не работает. Стабильно низкие баллы Availability указывают на частые поломки и оправдывают новое оборудование. Для окончательного решения потребуются дополнительные данные от программы CI о причинах сбоев и о том, были ли исчерпаны все разумные меры по увеличению времени безотказной работы.